Before making a tutorial, I’ve usually completed the project successfully a few times and know how to add my own pointers to help you get an extra-nice result.
Not this time, friends.
The sequence captured in these DIY Silicone Mold Making photos didn’t quite work out the way I needed it to, but I decided to go ahead and share my process because I think it would have worked for most purposes, and would probably have worked for my project (resin molding) if I’d had a bit more patience during the curing process. With that killer introduction out of the way, here’s my tutorial and recipe for creating this quick-dry, smooth-consistency DIY silicone mold making material.
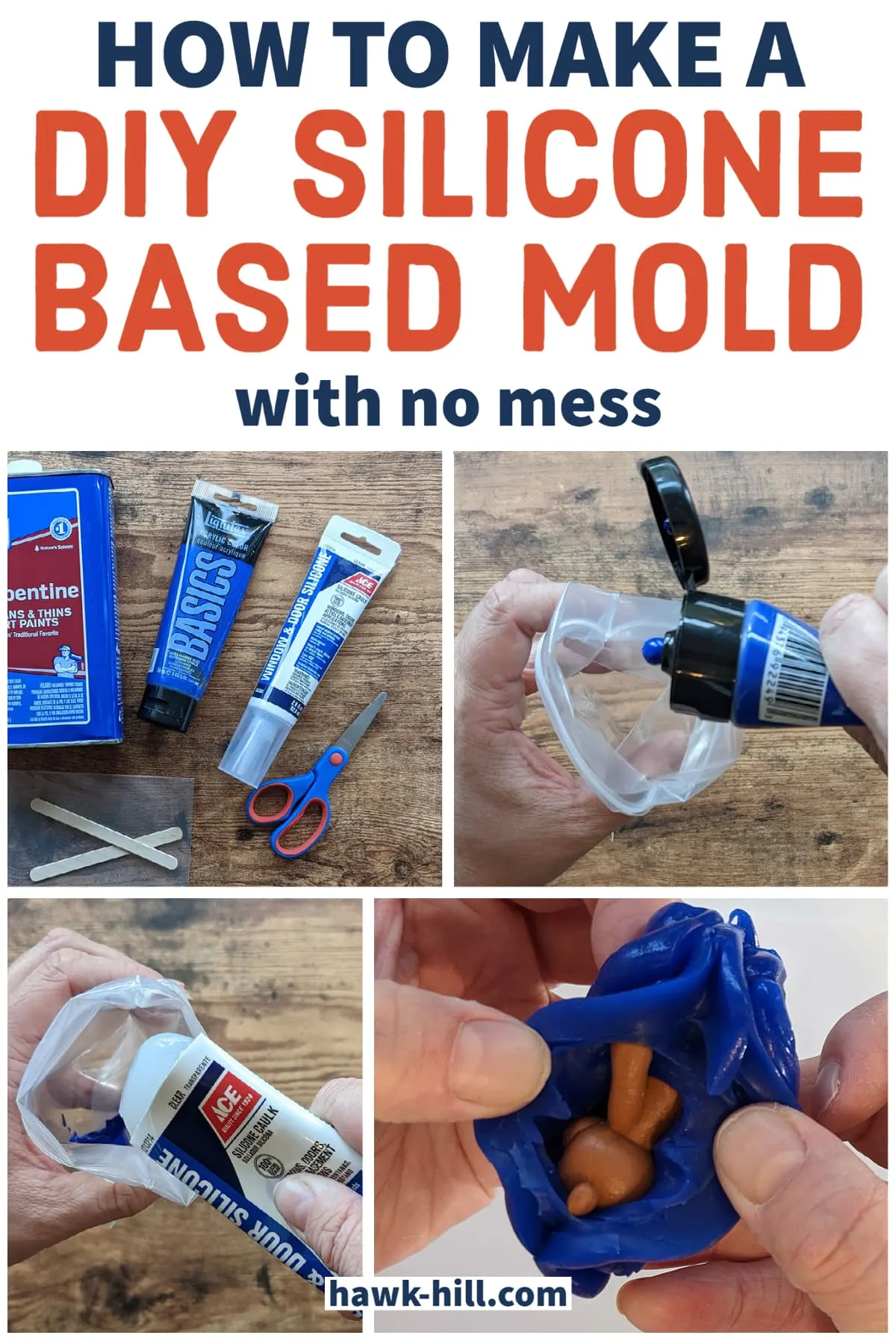
The following section may contain affiliate links. As an Amazon Associate, we earn from qualifying purchases.
Making Your Own Silicone Mold
Any silicone caulk labeled “100% silicone,” will work to create a mold for small to medium-sized objects- capturing detail in a reusable, easy to clean, flexible mold.
The problem? Pure silicone caulk is very thick and very goopy. This consistency makes it really hard to cast a mold without any bubbles or gaps in the silicone- Imagine trying to cast a mold in peanut butter and you’ll get the idea. This texture creates gaps and bubbles in the mold which leave ugly blister-like marks on the surface of cast objects when unmolded.
Solution: The internet-delivered several solutions for me: silicone caulk can be mixed with other ingredients to change the consistency without affecting the usability of the mold you make.
What You’ll Need for DIY Silicone Mold Making (Supply List):

- Disposable food prep gloves– keep this off your skin!
- An extremely well-ventilated work area (i.e. outdoors, see note below)
- Turpentine
- Acrylic paint (craft grade acrylic paint is fine and may actually work better because of the high water content)
- Sturdy freezer-type gallon-sized ziplock bags
- scissors
- 100% Silicone Caulk (If you’re making a larger mold and buying contractor-sized silicone tubes, you’ll also need a caulking gun)
- Wood craft sticks
Caution: This mold making method gives off potentially dangerous fumes. Work outdoors or in a mechanically vented room only. Do not attempt in a closed room. Wear a gas-filtering mask if needed. Be prepared to double-bag and dispose of the mixing bag and any extra mold material. Finished molds will have an odor and should be stored double-bagged or in sealed containers.
Step 1: Add Paint (Catalyst + Pigment) to Mixing Bag
Begin by placing a generous amount of acrylic paint into the heavy-duty zip bag. There’s no hard and fast recipe, but in this tutorial Ill be working with ratios, so use “one part” paint. To scale up or down, just consider one “part” a smaller or larger unit of measurement, i.e. teaspoon, tablespoon, cup, pint.
I add paint for two reasons: 1. added pigment makes it easier to visually gauge when the mold material is mixed and ready to pour, and makes it easier to get a sense of the thickness of the silicone in a particular area of the mold. 2. Normally, silicone is catalyzed to cure via exposure to moisture in the air. The addition of craft paint integrates moisture directly into the mix, which means your silicone mold will cure as quickly as one hour, instead of the 24 hours normally needed for pure silicone.

Step 2. Add Silicone
Add 8 parts 100% silicone caulk to mixing bag. Roll back the zipper-portion of the bag to help keep the seal clean.

Step 3. Turpentine as Thinner
Working outside or in a very well-ventilated area, and with a helper holding the bag (or using a sturdy prop and clip to hold it upright) add 2 parts turpentine to your mixture in the bag. For a more pourable silicone mold material, add an additional part turpentine, and test consistency after mixing (more turpentine can be added).

Step 4. Mix
With paint, silicone, and turpentine added, seal your bag and gentle squeezing to mix the materials. Keep your gloves on for this part, and work in a protected and well-ventilated area- even heavy-duty bags can manage to leak!
The addition of paint (a catalyst to speed hardening) also helps track how well mixed the DIY silicone mold mixture is:

mixing…

Step 5. Cut Bag
When you are ready to make your mold, snip off the tip of one corner of the bag. (I’m mixing a small batch in this round, but you can see below how a larger batch comes together in the same way)

Step 6: Pipe DIY Silicone Mold Material onto Object to be Molded
You can now use the heavy-duty zip bag as a piping bag. This will help you apply your silicone precisely to the item you are casting a mold of.
In this image, I’m demonstrating with a few small, but highly detailed toys.

Thinned down silicone and the easy application of the mixing bag turned piping bag makes it easy to carefully apply the silicone to delicate detail and fragile areas of my item to be molded.

Step 7. Cover Object with Mold Mixture
Carefully cover all surfaces and smooth to create a mold. You’ll want to carefully check for gaps in silicone (a bright contrasting color makes this easy!) so when you later pour your material to be molded it won’t leak out.

Step 9. Cure Mold
Allow to fully cure. Depending on humidity, the thickness of cast, and ingredient levels this may take anywhere from 1 hour to 1 day. When you can gently touch the surface and it firmly bounces back to touch without any hint of stickiness, you’re ready to unmold your cast object.
Let cure OUTSIDE in a sealed bag to minimize odor. Silicone is moisture-cured, not heat or air-cured, so the addition of the water-based paint provides everything the mixture needs to set.
Step 10. Cut Open Silicone Mold
Once the silicone is firm and springy, it’s ready to cut open. I let this mold site outside for three days to cure before slicing it open and tugging out the toy to reveal a perfect, detailed mold. Depending on the intricacy of your casting and the material that you’ll be using in the mold, you may want to cut the mold in half, as shown here, or simply make an incision in the top and pull your molded object free. The later method works especially well if you’ll be using your mold for working with a liquid media like resin, cement, or plaster.


A quick tip for easy unmolding of your art:
You’ll need (for casting objects):
- dish soap
- water
- cornstarch
- paintbrush
- paper coffee filter or folded paper towel
For easier uncasting of objects, begin by mixing 2-3 drops of dish soap in 2-3 tablespoons of water and mix thoroughly. Paint this mixture onto the object to be cast with a clean paintbrush. Allow to dry. Once dry, the surface should have a slightly textured, tacky surface feel. (if it doesn’t, apply another coat of soapy water and let dry).
Next, place 1-2 tablespoons of cornstarch into a porous package (a folded paper towel, a coffee filter, etc) and pat the package of cornstarch against the surface of the object. This should create a very light and even dusting of cornstarch across the surface, which makes most objects slide easily from the mold after casting.
Thanks for Reading!!!
I hope you can tell that I love DIY, researching the best affordable solutions for every-day problems opportunities and documenting / sharing solutions!🙌 Hawk-Hill.com is reader-supported.
☕ Hawk-Hill.com is reader-supported. If this article saved you time or money, please consider donating $1 to help me cover the cost of hosting this website OR If you appreciate this information and want to throw a “Thanks!” my way by buying me a coffee – I would Of Course appreciate it! :]
Reader Questions and Recommendations
Readers, do you have any favorite topics / posts? What would you like to read more about in the future? As I hope you can tell from this and other articles on my site, I really enjoy DIY / a good challenge, and I’m not afraid to roll up my sleeves to figure out a great, and hopefully simple 😁 solution. So please feel free to let me know in the comments below (or reach out via social media)!
Ok Really – I’ll try to wrap this up now😂
Finally, if you’d like to continue to learn about interesting DIY options as well as how YOU can tackle creative new projects consider checking out the latest and most popular articles listed on the Hawk-Hill Home Page. I’m always trying to enjoy and write about the creative side of life so please don’t be a stranger – check back often!😍
If you enjoyed this post you may also enjoy reading / perusing / devouring😊 one or all of these articles as well!
Caryn Karason
Sunday 21st of November 2021
Did you make a resin object from this mould afterwards? How well did the detail come out